The Zaccaria Maize Degerminator System: A Comprehensive Overview
- Facet Engineering
- Apr 7
- 8 min read
The Zaccaria maize degerminator system stands out as one of the most efficient and advanced systems available in the market today, consistently delivering a 99% clean product that eliminates the need for additional machinery in the processing chain. This remarkable efficiency stems from its innovative design, which integrates cutting-edge engineering principles with practical solutions tailored to the demands of modern maize processing. Whether the end goal is milling high-quality maize flour or producing samp (a coarse maize meal popular in various regions), this system offers a streamlined, cost-effective, and space-saving alternative to traditional methods.
The system is composed of several key components: a continuous conditioner, a horizontal degerminator, an extraction fan paired with a cyclone, and an optional dryer. Each element is meticulously engineered to work in harmony, ensuring that the maize kernels are processed with precision and minimal waste. Let’s explore the system’s operation in detail, filling in the gaps from the original description and expanding on its functionality, benefits, and implications for the maize processing industry.
The Process: From Raw Maize to Finished Product
The journey of maize through the Zaccaria system begins with the continuous conditioner, a critical component that sets the stage for effective degermination. Unlike older systems that rely on prolonged soaking or cumbersome holding bins, the Zaccaria approach is both dynamic and efficient. The process starts with moisture being absorbed into the maize prior to its exit from the conditioner and entry into the degerminator. This is achieved through an adjustable spread trough and a precisely controlled water flow. The trough ensures that the maize is evenly distributed, allowing each kernel to come into contact with the water in a uniform manner. This innovative contact mechanism replaces the need for traditional holding bins, which use large volumes of water and occupy significant floor space while adding unnecessary complexity to the process.
The continuous conditioner is a game-changer in maize processing. Traditional methods often involve soaking maize in holding bins for hours, a practice that not only consumes excessive water but also requires substantial storage infrastructure. In contrast, the Zaccaria conditioner adds the exact amount of water needed to each and every kernel in a short amount of time, typically within minutes. This precision saves floor space, reduces processing time, and conserves water, making it an environmentally friendly and cost-effective solution. As the maize moves horizontally through the conditioner, it emerges optimally moistened and ready for the next stage, without the delays or inefficiencies of older systems.
Once conditioned, the moistened maize enters the horizontal degerminator, the heart of the system. Here, the kernels are subjected to a high-speed geometric rotor, a sophisticated piece of engineering designed to maximize efficiency. The rotor forces the maize against special slotted scourer screens, which are uniquely contoured to scour the kernels effectively. The horizontal design of the degerminator is a significant improvement over earlier vertical models. In vertical degerminators, gravity pulls the maize through the machine quickly, limiting the time the kernels spend in contact with the screens. The horizontal configuration, however, ensures prolonged contact, allowing for more thorough removal of the germ and outer skin (pericarp). This results in a cleaner product with improved consistency and quality.
The degerminator’s screens are a marvel of design. The slotted scourer screens feature a textured surface that gently but effectively abrades the maize kernels, stripping away the germ and pericarp while leaving the endosperm, the starchy core of the kernel, intact. The machine is fully adjustable, enabling operators to fine-tune the scouring action to perfectly remove the germs and outer skin of the maize kernel exactly as required. This adaptability is crucial, as different maize varieties and end products (e.g., fine flour versus coarse samp) demand varying degrees of degermination. The product leaving the machine would not also require any further polishing, scouring, or aspiration but is instead ready for immediate milling or samp production. This eliminates the need for additional equipment, reducing both capital expenditure and operational costs.
The Output: Quality and Versatility
The result of this process is an end product that meets the highest standards of quality and versatility. The moisture level of the maize can be precisely controlled to suit the needs of downstream processes, whether that’s milling into flour or producing samp. The system achieves a high level of germ-free kernels, ensuring that the endosperm remains pure and free of unwanted components. This is particularly important for milling, where the presence of germ can introduce excess oil, affecting the shelf life and texture of the flour. Conversely, the germ itself retains a high level of oil, making it a valuable byproduct for oil extraction or animal feed. The outer skin is also efficiently removed, leaving behind an excellent superficial kernel with its mass endosperm intact, a perfect starting point for a range of maize-based products.
The quality of the output is a testament to the system’s engineering. By removing the germ and pericarp with such precision, the Zaccaria degerminator produces kernels that are visually appealing, structurally sound, and optimized for further processing. For samp production, where larger, intact endosperm pieces are desired, the system excels at delivering a coarse, clean product. For flour milling, the degerminated maize can be ground into a fine, consistent powder with minimal additional effort. This versatility makes the system a favorite among processors catering to diverse markets.
Byproduct Management: Efficiency and Value
The Zaccaria system doesn’t stop at producing a high-quality primary product, it also handles byproducts with remarkable efficiency. The germ and outer skin, once separated from the endosperm, pass through the screens and are collected in a hopper below the machine. This process is aided by an extraction system, which includes a fan and cyclone, keeping the machine under regulated pressure and containing any dust, a feature that is highly sought after in the industry. Dust control is a significant concern in maize processing, as airborne particles can pose health risks to workers and create sanitation challenges. The Zaccaria system’s extraction mechanism ensures a clean working environment while capturing valuable byproducts.
This extracted material, often referred to as hominy chop (or “horning chop” in some regions), is pneumatically removed from the machine and collected via the cyclone, where it is bagged off for later use. Hominy chop consists of the germ, pericarp, and small amounts of endosperm that pass through the screens. It is a nutrient-rich byproduct with multiple applications, including animal feed, industrial processing, or even as a base for fermented products in some cultures. By efficiently separating and collecting this material, the Zaccaria system adds value to the processing operation, turning what might otherwise be waste into a marketable commodity.
Advantages Over Traditional Systems
To fully appreciate the Zaccaria maize degerminator system, it’s worth comparing it to traditional degermination methods. Historically, maize processing relied heavily on vertical degerminators or manual methods, both of which had significant drawbacks. Vertical degerminators, while effective to a degree, suffered from limited screen contact time, resulting in incomplete germ removal and inconsistent product quality. Manual methods, still used in some small-scale operations, are labor-intensive, time-consuming, and prone to human error. Both approaches often required additional machinery, such as polishers, aspirators, or secondary degerminators, to achieve a clean product, driving up costs and complexity.

The Zaccaria system, by contrast, consolidates these steps into a single, streamlined process. The continuous conditioner eliminates the need for holding bins, which in traditional setups could occupy dozens of square meters and require hours of soaking time. The horizontal degerminator, with its adjustable rotor and screens, outperforms vertical models in both efficiency and precision. The integrated extraction system further enhances the system’s appeal by managing byproducts and dust without additional equipment. The optional dryer, while not always necessary, provides flexibility for processors who need to adjust moisture levels post-degermination, such as in humid climates or for specific milling requirements.
From a resource perspective, the savings are substantial. The conditioner’s water efficiency reduces consumption compared to soaking methods, aligning with growing demands for sustainable agricultural practices. The compact design minimizes floor space, a critical consideration for facilities where real estate is at a premium. And the elimination of downstream machinery cuts energy use and maintenance costs, making the system economically attractive for both large-scale processors and smaller operations looking to modernize.
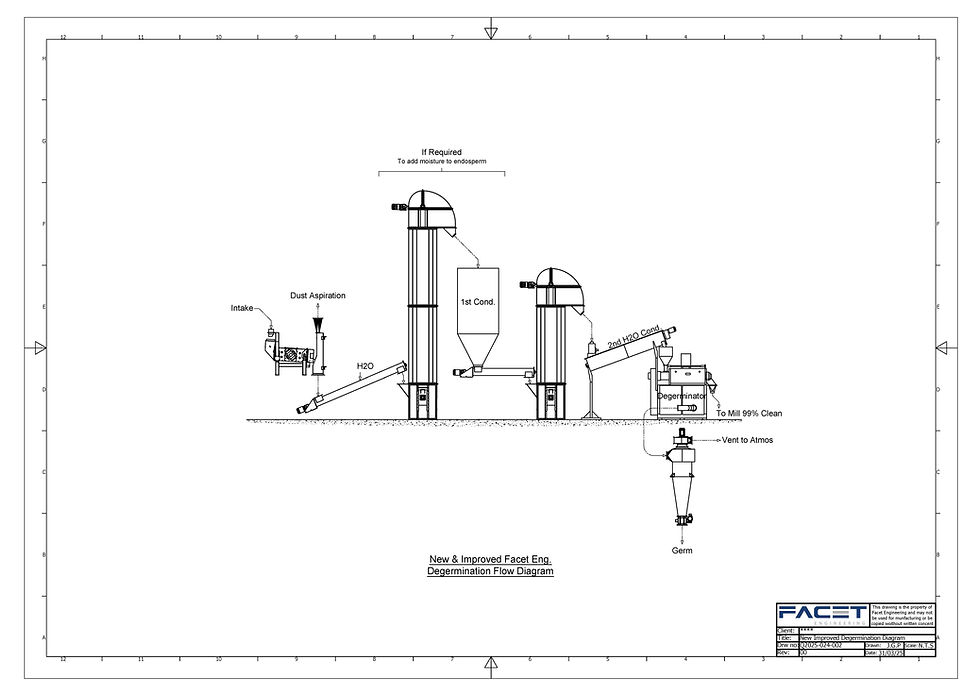
Applications and Market Impact
The Zaccaria maize degerminator system is well-suited to a wide range of applications, reflecting its versatility and precision. In regions where maize is a staple crop, such as parts of Africa, Latin America, and North America, the system supports the production of high-quality food products. For example, in South Africa, where samp and mealie meal are dietary staples, the system’s ability to produce clean, coarse endosperm with minimal germ content is a major advantage. A strength leveraged by Facet Engineering South Africa, an agent for Zaccaria, based in Brazil. Facet brings this Brazilian-engineered technology to the region, enhancing local processing capabilities. In Mexico, where maize flour is used for tortillas, the degerminated kernels provide a consistent base for fine milling. Even in industrial settings, such as ethanol production or snack food manufacturing, the system’s output meets stringent quality standards.
The market impact of the Zaccaria system is significant. As global demand for maize products grows, driven by population increases and dietary shifts, processors are under pressure to improve efficiency and reduce costs. The Zaccaria system meets these needs head-on, offering a solution that boosts throughput, enhances product quality, and lowers operational overhead. Its ability to produce a 99% clean product without additional machinery positions it as a leader in the industry, challenging competitors to innovate or risk obsolescence.
Technical Specifications and Design Philosophy
While specific technical details (e.g., rotor speed, screen mesh size, or throughput capacity) would depend on the model and manufacturer documentation, the Zaccaria system’s design philosophy is clear: simplicity, precision, and adaptability. The continuous conditioner exemplifies this by replacing bulky, static bins with a dynamic, flow-through process. The horizontal degerminator’s adjustable settings allow operators to tailor the machine to specific maize varieties or product requirements, a level of customization that rigid, older systems can’t match. The extraction system, with its fan and cyclone, reflects a commitment to workplace safety and byproduct valorization.
The materials used in the system are stainless steel, chosen for longevity and resistance to wear, given the abrasive nature of maize processing. The geometric rotor, a standout feature, is engineered to balance speed and force, ensuring that kernels are scoured effectively without excessive breakage. This attention to detail underscores the system’s reliability, a key factor for processors who depend on uninterrupted operation during peak harvest seasons.
Challenges and Considerations
No system is without challenges, and the Zaccaria maize degerminator is no exception. Its reliance on precise water control in the conditioner requires consistent maintenance to prevent clogging or uneven moisture distribution. The high-speed rotor, while efficient, may demand regular inspection to ensure optimal performance, especially when processing tougher maize varieties. And while the system reduces the need for additional machinery, its upfront cost could be a barrier for small-scale processors transitioning from manual or outdated methods.
However, these challenges are outweighed by the system’s benefits. Maintenance requirements are standard for industrial equipment, and the long-term savings in water, space, and energy offset the initial investment. For small operators, financing options or cooperative ownership models could make adoption feasible, particularly in regions where maize processing is a communal activity.
Conclusion: A Step Forward in Maize Processing
The Zaccaria maize degerminator system represents a significant advancement in the field of maize processing, blending efficiency, quality, and sustainability into a single, cohesive package. From the continuous conditioner’s water-saving design to the horizontal degerminator’s precision scouring, every component is engineered to deliver a 99% clean product with minimal fuss. The system’s ability to eliminate downstream machinery, manage byproducts effectively, and adapt to diverse applications makes it a standout choice for processors worldwide.
With maize remaining a cornerstone of global agriculture, the Zaccaria system is poised to play a pivotal role in meeting the industry’s evolving needs. Whether you’re a large-scale miller aiming to optimize production or a regional processor seeking to upgrade your operation, this system offers a compelling solution, one that promises not just efficiency, but excellence.
Comments